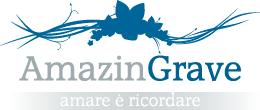
MENU
TUTTI GLI ORDINI EFFETTUATI DAL 19 DICEMBRE,
VERRANNO PRESI IN CARICO DAL 6 GENNAIO
Prezzi IVA Inclusa
Spedizione Gratis a Partire da 135€
Metodi di Pagamento Accettati:
PayPal
Bonifico Bancario
Carte di Credito
Alla Consegna
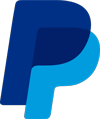
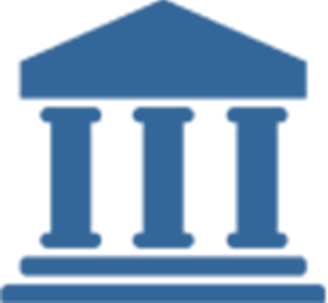
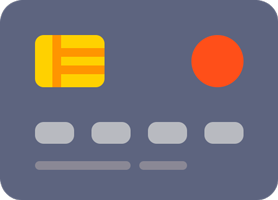
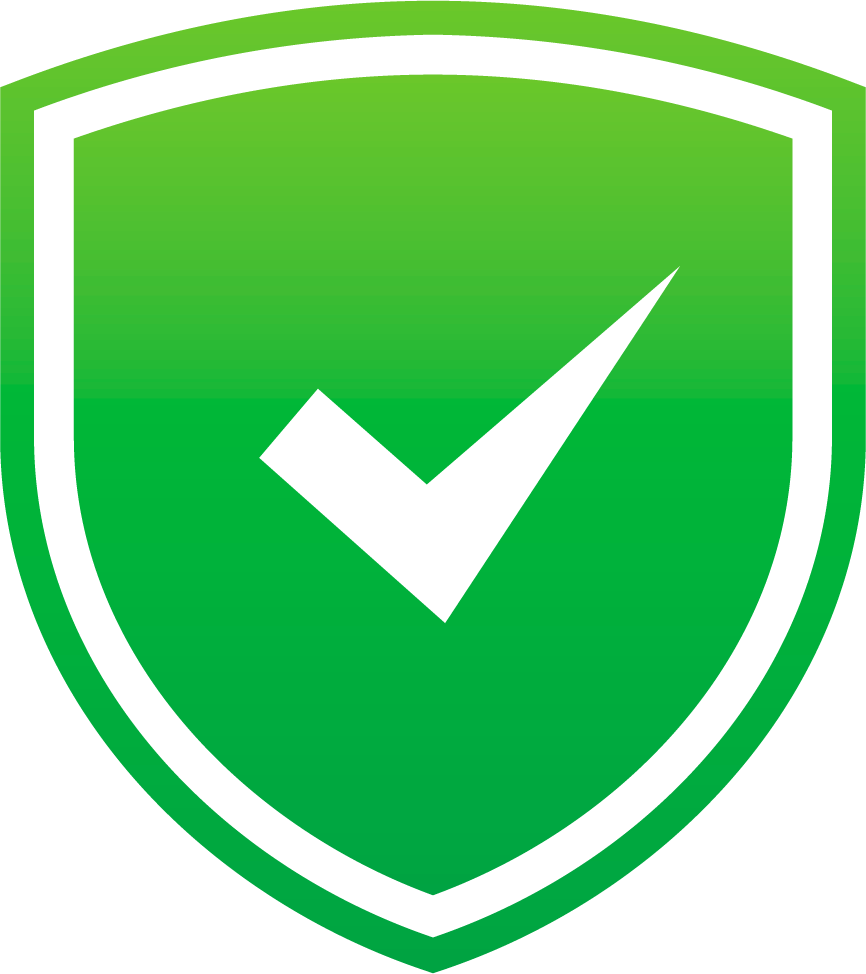
TIPI DI FUSIONE
LA FUSIONE A CERA PERSA
La fusione a cera persa è una tecnica millenaria utilizzata per la realizzazione di manufatti in bronzo.
La fonderia a cera persa si basa sulla colatura di metallo fuso all’interno di una forma negativa; quindi si esegue in cera la scultura che si vuole trasformare in bronzo, ma vuota. La cera deve avere cioè solo lo spessore che si vuole che abbiano le pareti di bronzo (o di altro metallo) che costituiranno la scultura una volta fusa in metallo. E’ una tecnologia antica che è stata sviluppata negli anni e che oggi, oltre che per opere artistiche, è molto adoperata nell’industria avendo raggiunto elevatissimi livelli tecnologici. E’, infatti, sempre utilizzata quando si richiede un pezzo di massima precisione e quando l’esecuzione tradizionale comporterebbe tempi di lavoro complicati e lunghi. Oggi, per esempio, sono costruiti in cera persa gli elementi più importanti dei motori a reazione degli aerei. Le pale interne delle turbine, devono sopportare velocità periferiche di circa 450m/s raggiungono temperature superiori ai 1200 gradi con velocità di deflusso di 750 m/s. Il sistema di raffreddamento utilizza minuscoli micro fori e canali di spessore infinitesimale che possono essere fabbricati soltanto con il procedimento della cera persa.
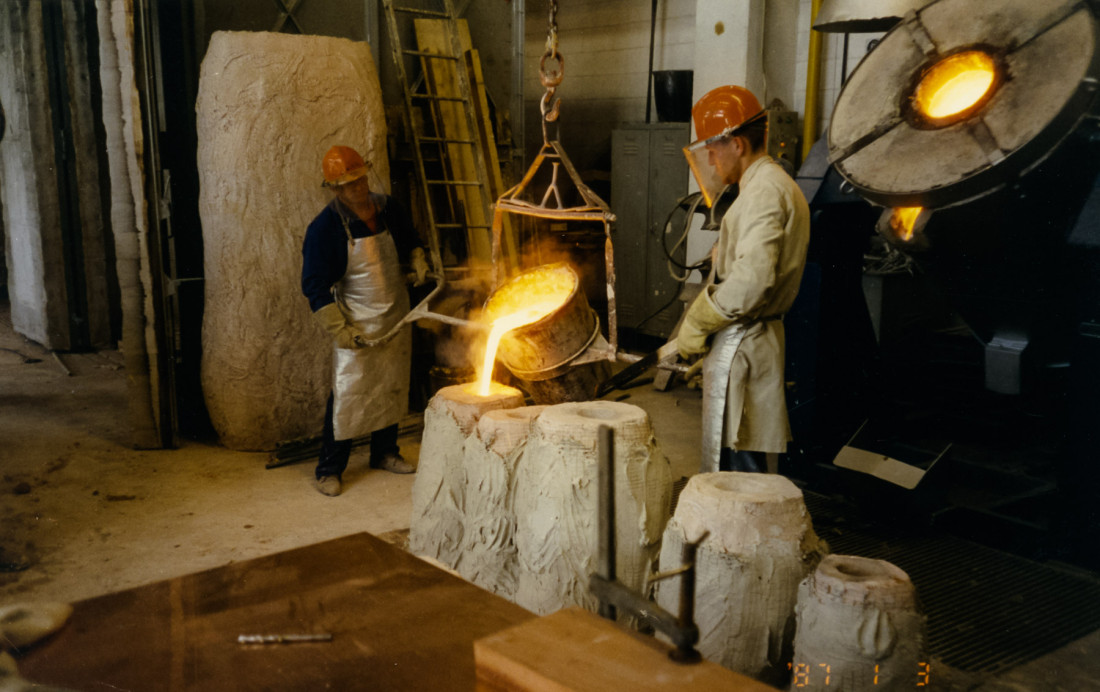
La fusione a cera persa è una tecnica scultorea originariamente introdotta nell'età del bronzo, già dal 3500 a.C. dalle popolazioni sarde, e che nei secoli ha conosciuto una notevole fioritura, soprattutto nell’arte sarda (vedi realizzazioni di statue in bronzo), e nell'arte greca, romana e nella scultura monumentale, dalla prima derivate.
Esistono due modi di servirsi di questa tecnica:
Modo indiretto - Consiste nel creare un modello di cera e utilizzarlo per farne uno stampo di argilla. Praticando due fori sullo stampo, uno in alto e uno in basso si fa uscire la cera scaldandola e si versa del bronzo fuso al suo posto. Se ne ricava un modello identico a quello di cera.
Modo diretto - Assomiglia al primo metodo, ma il modello di cera è realizzato su di un altro in creta in modo che la statua finale sia vuota all'interno (o meglio, contenga solamente argilla per limitare il peso e la quantità di metallo usata).
FUSIONE A TERRA
La lavorazione classica di fonderia è quella della colata in terra, per via del fatto che il metallo fuso viene colato in uno stampo composto da una terra speciale, detta terra da fonderia, che alla fine del processo verrà rotta per poterne estrarre il pezzo.
Le terre usate, perdono le loro qualità per effetto dell'alta temperatura, pertanto è possibile riutilizzarle solamente dopo un opportuno trattamento.
Questa tecnica prevede la realizzazione di uno stampo mediante l’utilizzo di un particolare tipo di terra, chiamata, appunto, terra per stampi. Si tratta, di fatto, di un metodo usa e getta poiché, dopo la colata del metallo fuso e la sua successiva solidificazione, lo stampo viene distrutto per estrarre il pezzo.
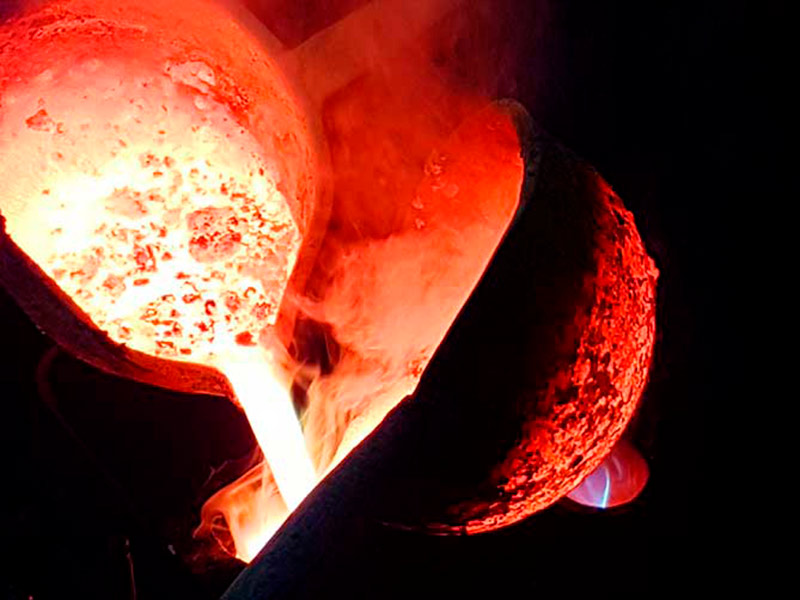
Ma come si costruisce uno stampo in sabbia? Ovviamente, occorre disporre di una matrice da posizionare all’interno del telaio in cui viene disposta la sabbia. Una volta compattata la terra, la matrice viene rimossa affinché nello spazio rimasto vuoto possa esser fatto colare il metallo fuso. Questa operazione viene preceduta dalla creazione di una serie di canali di colata, alcuni dei quali condurranno il metallo all’interno dello stampo mentre altri fungeranno da materozze.
In seguito alla colata, lo stampo viene rotto per liberare l’oggetto realizzato.
Questo metodo è il più economico e viene usato prevalentemente per la realizzazione di pezzi unici o in piccola serie. Come puoi ben immaginare, adottare questa tecnica per produrre centinaia o migliaia di componenti metallici non sarebbe molto conveniente, ed è per questo che esistono soluzioni alternative alla fusione in sabbia.
PRESSOFUSIONE
È chiamata anche pressocolata e prevede la fusione del metallo, ad esempio nel caso della pressofusione acciaio, il quale viene poi iniettato all’interno di uno stampo metallico, ad altissima pressione. Si parla di una procedura antica, risalente al 1800, messa a punto inizialmente negli Stati Uniti e che ancora oggi appare indispensabile durante le fasi di produzione industriale per ottenere oggetti e componentistica delle forme più disparate, con un altissimo grado di ripetibilità. Il basso costo e la versatilità del processo lo rendono appetibile anche per le aziende attuali, quindi è bene imparare a conoscere meglio la procedura di pressofusione analizzando i seguenti punti:
Si sceglie la pressofusione soprattutto se si ha intenzione di realizzare oggetti in acciaio e alluminio. Il processo presuppone come detto la creazione di uno stampo e l’inserimento del metallo fuso al suo interno, sfruttando un sistema di canali, la forza pressoria e un sistema di raffreddamento. Per ciò che riguarda la pressione questa viene tenuta costante fino alla solidificazione del metallo trattato, affiancando a ciò il contemporaneo utilizzo della forza delle presse, che garantisce una chiusura ermetica dello stampo. L’oggetto viene poi raffreddato per mezzo dell’inserimento di liquido tramite il suddetto sistema di canali. A questo fa seguito la fase di apertura dello stampo, con i due semi-stampi che vengono separati e consentono di prelevare l’oggetto appena creato.